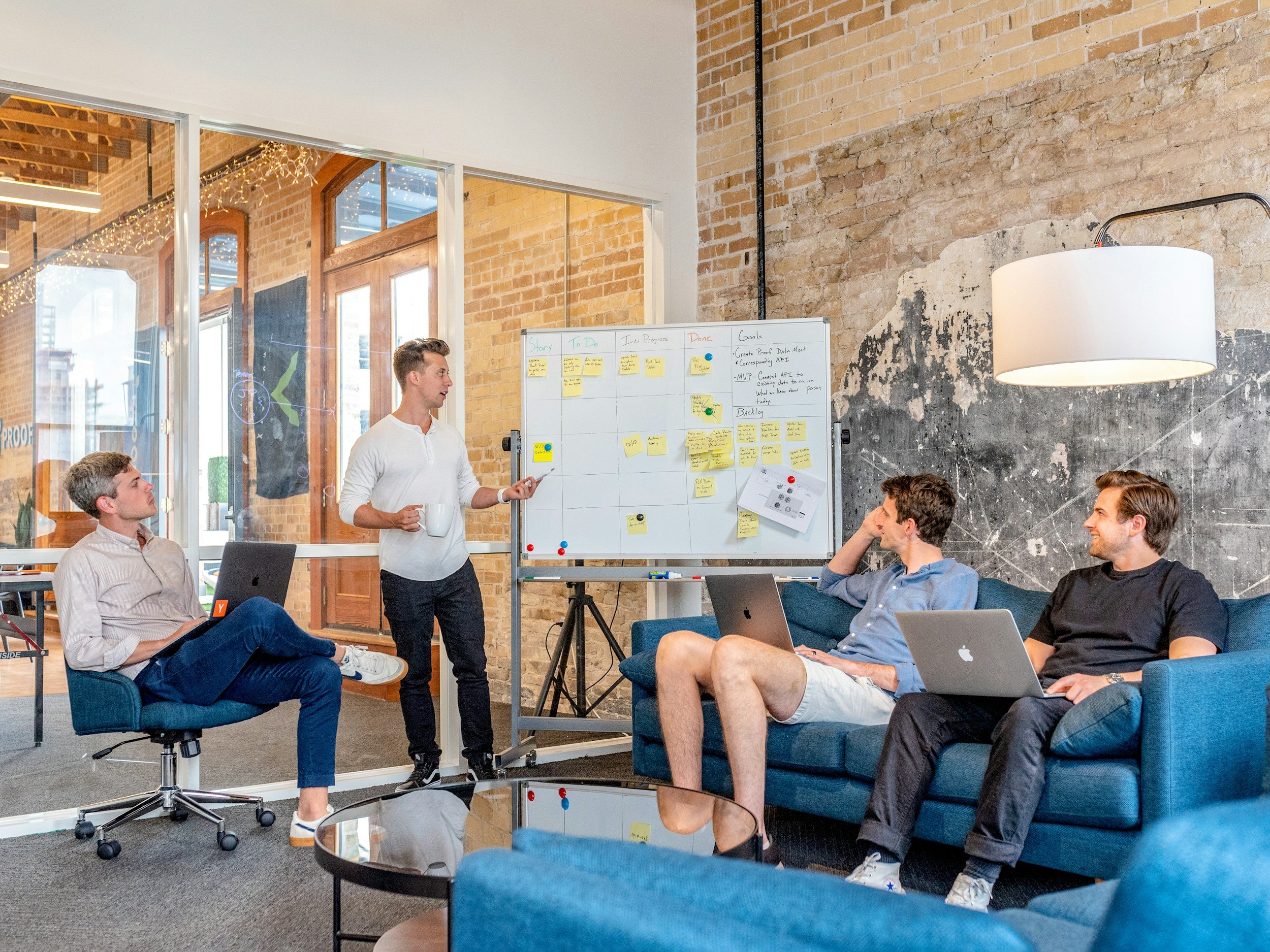
Operational Support
Operational Support
Our Operational Support Services are built to help companies navigate the complexity of regulated environments while maximizing efficiency, quality, and scalability. We work hands-on with your team to strengthen internal systems, improve day-to-day execution, and resolve operational challenges that hinder growth.
Whether you’re launching a new facility, scaling production, or addressing inefficiencies in existing workflows, we provide practical, actionable support across all phases of your operation. Our approach combines industry best practices, technical expertise, and real-time problem-solving to deliver results that are measurable and sustainable.
Services include:
Workflow and process optimization across manufacturing, packaging, inventory, and fulfillment
Development and implementation of SOPs, quality systems, and operational policies
Cross-functional alignment between departments (e.g., production, QA, compliance, facilities)
Resource planning and labor optimization strategies
Operational readiness assessments and gap remediation
Scaling support for new product lines, site expansions, or contract manufacturing partnerships
Our team embeds with yours to bridge the gap between strategic goals and operational execution — giving you the tools, systems, and support to run a smarter, safer, and more efficient business.
-
Demand Planning - Forecasting customer demand to optimize inventory and production levels
Inventory Systems - Managing stock levels to ensure supply meets demand efficiently
KPI Development - Creating key performance indicators to measure and monitor the success of business objectives.
Sales and Operations Planning (S&OP) - Aligning sales, production, and inventory plans to balance supply and demand
-
We can assist with planning, executing, and overseeing a variety of projects to achieve specific goals within scope, time, and budget.
-
Expert audit consulting services to ensure compliance, enhance safety, and optimize operational efficiency.
-
We can provide product guidance for a new launch, assist with genetics sourcing, or even assist with supply chain challenges or vendor setup.
-
We can assist with implementing lean manufacturing systems into your operation in order to reduce waste and improve efficiency in your production process.
-
Integrate cutting-edge automation into your processes
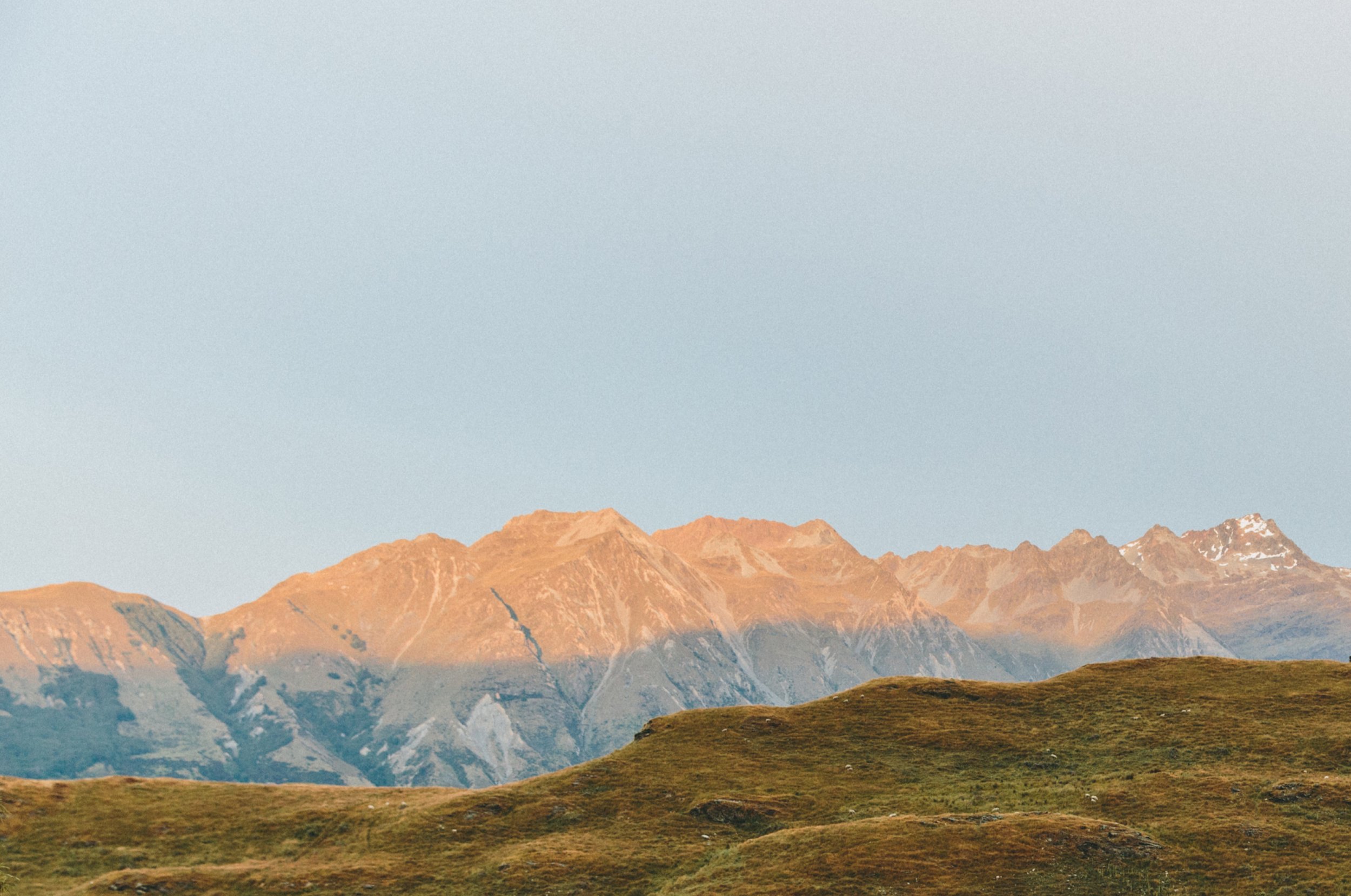